大型 高效 環保
瀏覽:次|評論:0條 [收藏] [評論]
近年來,大型燒結機在我國陸續得到使用,使燒結礦產量增加、質量提高。鋼鐵行業的激烈競爭,促使燒結工序不斷開發和應用節能降耗技術,同時由于國家對環保要求的日趨嚴格,燒結工序的環保技…
近年來,大型燒結機在我國陸續得到使用,使燒結礦產量增加、質量提高。鋼鐵行業的激烈競爭,促使燒結工序不斷開發和應用節能降耗技術,同時由于國家對環保要求的日趨嚴格,燒結工序的環保技術也得到重視和發展,越來越多的燒結煙氣凈化裝置進入建設和運行階段。
我國燒結業近年來出現一批500m2以上的大型自動化燒結機,實現了燒結過程精細化和自動化控制,對增加燒結礦產量、改善燒結礦質量起到良好的推動作用。同時伴隨著厚料層燒結、燒結余熱利用和燒結添加劑等技術的研究和應用,燒結工序的能耗和成本也得到降低。
為滿足我國燒結行業環保的要求,燒結煙氣脫硫技術在眾多鋼廠逐漸得到應用,但目前我國運行的燒結煙氣脫硫裝置呈現出工藝技術多樣、脫硫效果不穩定等問題,新建燒結煙氣脫硫裝置須要充分調研和考察各種技術的優劣,選擇適用自身特點、成本低、最好能夠具有多組分污染物脫除效果的技術和裝置。
大型自動化燒結機得到應用
大型燒結機具有單位產量投資低、技術經濟指標好等優點,而且產品質量好,勞動生產率高,能實現顯著的經濟效益。當今設計投產的大型燒結機一般都配有較先進的自動控制系統,不但能降低人工勞動強度,減少人工成本,而且能夠實現人工難以達到的操作水平,滿足燒結過程的精細化與穩定化控制要求,進而提升燒結各項指標。
隨著我國煉鐵高爐的大型化,為滿足高爐生產需要,涌現出一批500m2以上的大型自動化燒結機。太鋼660m2燒結機于2010年投產,是目前國內燒結面積最大、裝備最先進的燒結機,采用自行研制的燒結綜合控制技術,可實現過程控制的標準化和智能化。我國部分500m2及以上大型燒結機統計情況如表1所示。
節能重點在降能耗與余熱回收利用
燒結工序的節能利用主要有降低燒結工序能耗和燒結余熱回收利用兩方面。燒結工序能耗主要包括固體燃料消耗、電力消耗和點火煤氣消耗。目前降低燒結工序能耗的節能技術和措施主要有:優化配礦、預熱混合料、厚料層燒結、熱風燒結、減少燒結機漏風和提高點火質量等,我國多數鋼廠都采用此類技術措施以達到燒結節能目的。
燒結余熱回收水平較低是造成我國燒結工序能耗較高的一個因素。燒結余熱回收利用主要是針對燒結煙氣和燒結礦顯熱兩方面。燒結煙氣溫度隨燒結機風箱位置不同而有較大差異,其成分復雜、含濕量大、攜帶大量粉塵,而且由于未預留回收裝置或者改造困難等原因,這部分余熱回收利用得很少。日本、德國和奧地利等國外的部分鋼廠采用煙氣循環技術處理此部分廢氣,可以顯著減少燒結工藝中的廢氣排放總量和污染物排放量,降低燒結工藝的能耗,但存在煙氣含氧量低、對后續設備腐蝕等問題。我國燒結廠主要針對燒結機尾部高溫段煙氣回收其熱能,如三鋼、安鋼等利用燒結煙道廢氣余熱進行發電等。近年來國內也開始研究燒結煙氣循環技術,國內首個燒結廢氣余熱循環利用項目示范工程在寶鋼集團寧波鋼鐵公司建成投運。
燒結礦顯熱回收利用主要針對燒結礦冷卻過程產生的熱廢氣進行熱量回收,目前在國內應用較多,技術裝備比較成熟,主要有以下幾種方式:一是替代或者預熱點火的助燃空氣,或者進行熱風燒結,改善燒結礦質量,如濟鋼利用冷卻機的中溫段熱廢氣進行熱風點火和熱風燒結;二是利用燒結余熱回收蒸汽,用于預熱燒結混合料或者廠內直接利用,如首鋼京唐燒結廠、長鋼等;三是余熱回收發電,將冷卻燒結礦產生的熱廢氣引入余熱鍋爐產生蒸汽,再通過蒸汽推動汽輪機帶動發電機發電,國內多采用“多爐帶一機”的發電方式,如馬鋼、唐鋼等。
煙氣脫硫工藝繁多亟須優化
燒結煙氣凈化處理在我國目前主要是推行脫硫裝置,《鋼鐵工業“十二五”發展規劃》要求:到“十二五”末,重點統計鋼企噸鋼二氧化硫排放量不超過1kg,燒結機全部加裝煙氣脫硫和余熱回收裝置,鼓勵實施脫硝改造。燒結脫硫技術采用的工藝種類繁多,主要分為濕法、干法、半干法。濕法脫硫主要包括石灰石-石膏法、雙堿法、氨吸收法、海水法和氫氧化鎂法等,干法脫硫包括活性炭吸附法、煙氣循環流化床干法、密相干塔法等,半干法脫硫包括噴霧干燥法(SDA)、增濕灰循環脫硫法(NID)、循環流化床脫硫法(CFB) 和MEROS法(Maximized Emission Reduction of Sintering)等。我國部分400m2以上大型燒結機煙氣脫硫工藝統計如表2所示。
我國在線生產運行的燒結煙氣脫硫工藝有多種,均有各自的優缺點,沒有形成一種主流工藝,且存在脫硫系統脫硫率不高、運行成本高且不穩定、副產物利用困難等問題。針對燒結煙氣的特點,開發適應性強、技術經濟指標先進、運行安全可靠的燒結煙氣脫硫技術,對于我國鋼鐵企業的燒結煙氣治理具有重要意義。
厚料層燒結節能增效重在控制
厚料層燒結以燒結料層自動蓄熱理論為基礎,能夠起到降低固體燃料消耗、改善燒結礦強度、提高成品率等作用,使其成為燒結生產長期以來的追求目標。特別是近年來,超厚料層燒結技術(≥800mm)的工業實踐成功,預示著此技術在國內的應用日趨成熟。馬鋼三鐵總廠在兩臺360m2燒結機上實現了900mm超厚料層均質燒結。此項技術的實施,使得燒結工序的綜合技術經濟指標顯著改善,有著明顯的節能增效作用,同時也實現了燒結礦質量的改善。
厚料層燒結可以有效利用料層的自動蓄熱作用,降低燒結固體燃料消耗和總熱量消耗。但隨著料層厚度的增加,料層透氣性下降,燒結過程下部料層濕度增加,容易過濕,垂直方向各層燒結礦不僅成分、粒度、堿度等變化較大,而且燒結礦轉鼓強度及冶金性能也有明顯差異。厚料層燒結的主要控制措施為:穩定燒結原料組成,優化混勻制粒、布料和抽風燒結等過程的工藝參數,以增加料層透氣性、改善上下層熱量分布。熔劑和燃料的粒度組成及添加方式等對厚料層燒結也具有一定的改善作用,近年來得到關注和研究。
富氧燒結增產提質有待工業化應用
2010年韓國浦項開發出富氧燒結技術,引起廣泛關注。此技術通過在燒結料層的不同位置吹入一定量的氧氣,提高焦粉燃燒率,加快料層的升溫速度,有效解決料層上部區域熱量不足的問題,改善燒結礦質量,提高燒結機利用系數。
我國關于富氧燒結的研究主要是增加點火空氣或燒結空氣中的氧含量,發現富氧燒結可以提高產量,每富氧1%可以增產8.45%,具有良好的經濟效益;而且能夠降低燒結點火能耗和減少CO2的排放量,燒結料層表面固體燃料的利用率提高,可獲得良好的燒結礦產量和質量指標。
我國鋼廠近年來進行了部分富氧燒結工業化試驗,為富氧燒結技術的研究積累了一定的實踐經驗。梅鋼曾在其3號燒結機進行富氧燒結研究,試驗由富氧點火和向燒結料層吹氧兩部分組成,即向點火助燃空氣和點火后的燒結料層表面增氧。結果表明,富氧點火或富氧燒結能夠改善燃料利用率,改善燒結礦強度和粒度組成,降低返礦率。韶鋼也曾在其360m2燒結機上進行過富氧燒結試驗,結果表明富氧燒結對燒結礦增產、燒結節能和燒結礦質量改善均有明顯效果。南通寶鋼通過燒結機富氧點火實踐,實現了提高燒結點火溫度、降低固體燃耗和減少返礦量等良好效果。
燒結配用添加劑提質降本要因地制宜
隨著鐵礦資源價格上升,為降低成本,各鋼廠積極開發配用各種經濟鐵礦資源,導致燒結工序出現固體燃耗增加、燒結礦質量降低等問題。燒結添加劑逐漸成為改善燒結礦質量、降低燒結成本的一個研究方向,目前研究和應用較多的燒結添加劑為CaCl2和各種復合添加劑。
燒結礦噴灑CaCl2溶液,是目前鋼廠公認的可以改善燒結礦的低溫還原粉化性能的方法,許多鋼廠采用此項技術,如寶鋼、萊鋼等。其主要機理為:CaCl2覆蓋在燒結礦的表層,抑制或延緩燒結礦中的α-Fe2O3(六方晶格)向γ- Fe2O3(立方晶格)反應,減少或避免晶格轉變造成的燒結礦破裂和粉碎,從而改善高爐爐料透氣性,利于高爐穩定順行。但CaCl2的添加會使荷重熔滴性能變差,導致高爐中、下部的透氣性變差,且噴灑的CaCl2在高爐內高溫區域會跟燒結礦中的SiO2反應生成HCl,腐蝕高爐爐壁和爐頂區域,縮短高爐使用壽命。燒結礦噴灑CaCl2溶液對高爐運行有利也有弊,每個鋼企的自身情況不同,是否噴灑CaCl2溶液,須要根據各自的配礦結構、燒結礦性能和高爐特點等情況經試驗后確定。
復合增效劑,一般由增氧劑、催化劑、強化劑等組成,通過直接添加或者溶解后噴灑到燃料表面,能夠在燒結過程中催化助燃固體燃料、降低固體消耗,同時增強氧化性氣氛,促進固、液相的結合與結晶,改善燒結礦質量。經唐鋼、首鋼、邯鋼、南鋼等國內眾多鋼廠的試驗和應用證明,在燒結混合料中添加0.03%~0.05%的增效劑,就能顯著改善燒結礦質量技術指標和經濟效益。
為減少燒結煙氣含硫量,在燒結過程添加脫硫劑也得到了部分研究。此類添加劑試驗發現,其雖然能實現燒結煙氣脫硫效果,但是會造成燒結礦質量下降、煙氣除塵灰含硫量增加、除塵設備運行難度增大等問題,尚未得到工業推廣應用。
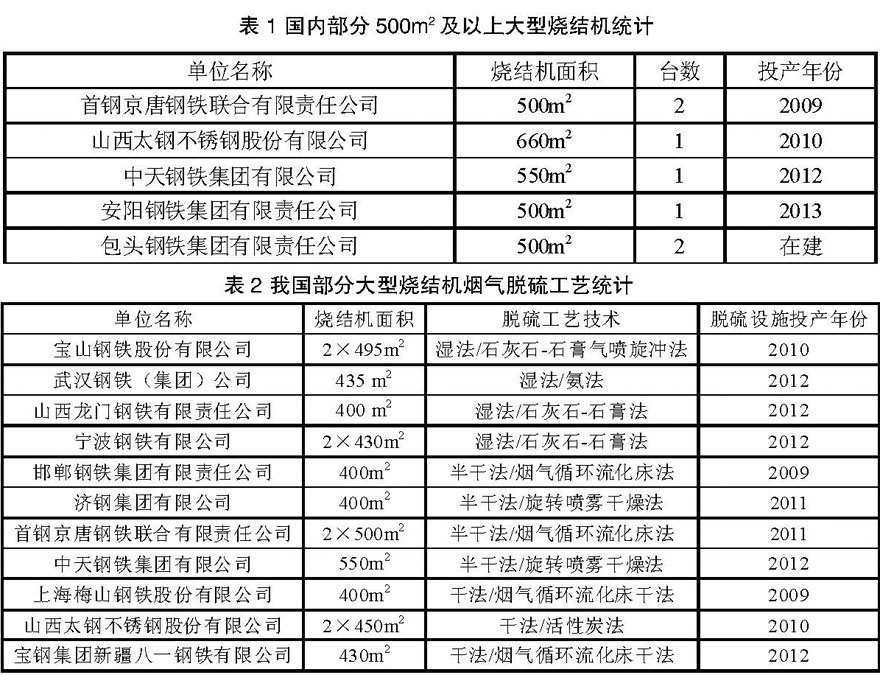
- [騰訊]
- 關鍵字:無