寶鋼燒結固體燃料粒度控制探索與實踐
瀏覽:次|評論:0條 [收藏] [評論]
袁 兵 馬洛文 王躍飛 魯 健 摘 要 燒結固體燃料破碎過程受多方面因素的影響,具有粒度波動性較大及人為影響大的特點。根據固體燃料燃燒理論和顆粒比表面積變化規律,找出了燃料粒度波動…
袁 兵 馬洛文 王躍飛 魯 健
摘 要 燒結固體燃料破碎過程受多方面因素的影響,具有粒度波動性較大及人為影響大的特點。根據固體燃料燃燒理論和顆粒比表面積變化規律,找出了燃料粒度波動對燒結過程的影響,結合寶鋼燒結的實際條件和生產經驗,對固體燃料粒度波動做到了較準確的判斷,并制定了相應的生產調整措施,確保了寶鋼燒結生產的穩定,達到了降低固體能耗的目的。
關鍵詞 固體燃料 粒度波動 燒結參數 調整 穩定生產
1 概 述
國內大多數燒結廠都是采用對輥、四輥破碎機對煤進行破碎。寶鋼股份設計時,因考慮全焦燒結,故采用棒磨機進行燃料破碎。近年來,為降低燒結成本,無煙煤的使用量逐步增加,焦炭和無煙煤使用同一系統進行破碎。寶鋼固體燃料破碎系統為閉路破碎篩分系統,主要由粗焦槽、粗焦篩、粉焦篩、中繼槽、反擊式破碎機、棒磨機以及傳輸皮帶等設備構成。從原料堆場、煉焦工序和高爐工序輸送來的固體燃料(主要是粗焦和無煙煤) 貯存在兩個容積為
固體燃料粒度主要是通過粗焦篩、粉焦篩篩網孔徑,以及棒磨機流量等手段進行控制。為了減小固體燃料粒度波動,我們特制定了棒磨機加棒周期管理制度,并定期對篩網破損情況進行檢查。同時,按每臺破碎機每個班各取一個焦粉、煤粉樣,進行粒度分析,并通過L3 系統及時向生產方人員反饋粒度數據,加強對固體燃料粒度的控制。
2 固體燃料粒度變化對燒結生產的影響
盡管采取了上述措施來穩定固體燃料粒度,但實際生產中,燃料破碎后,其粒度仍然會出現波動。這主要體現在兩個方面,即平均粒度(M1S) 和粒度分布維數k (表示顆粒組成的集中和均勻特性) 發生波動。粒度分布維數k 的大小與顆粒的粉碎概率和粉碎相似有關,反映了實際顆粒分布與平均粒度之間的相似程度(k在0~1 之間取值) 。圖1 和圖2 是2008 年寶鋼1 號、2 號燒結機固體燃料平均粒度的統計。
4.3 燒結機頭部風箱開閉優化控制
針對固體燃料粒度的異常波動,也可通過調節保溫爐末端風箱支管閘門(一般為5 # 風箱) 開度,有效地調節燒結過程前后的氣流分布,延緩或加速焦粉在燒結過程中的燃燒速度。其開度視焦粉粒度決定,焦粉粒度越粗,5 # 風箱閘門開度應越大。風箱開閉控制的關鍵,是要保持大煙道內氣體的平均壓力(負壓) 在較低水平,BTP 溫度和位置比較穩定。負壓越高,風支管閘門開度應越大。就我廠的情況而言,其指導性開度列于表4 。
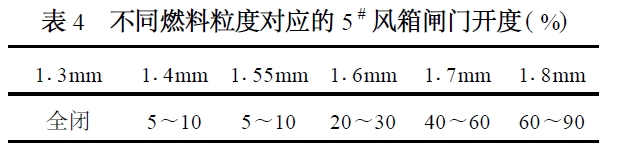
4.4 抽風風量優化控制
寶鋼燒結機設計為雙主排抽風系統,一主排風機負責對燒結機頭尾部抽風,一主排負責對燒結機中間部分進行抽風。為了優化和平衡兩主排抽風風量,在23 對風箱中設置了部分可切換風箱,用于調節風量,具體分布見表5。在固體燃料粒度發生波動期間,炭的燃燒速度加快或者延長,影響到燒結帶寬度和整個料層的透氣性。對此,可適當增加或減少燒結機中間部分的抽風風量,平衡燒結過程的風量分布,穩定燒結過程。
4.5 控制效果
采取上述措施后,可將固體燃料粒度波動時的隨機經驗控制轉變為理性分析型調整,對于燒結控制的精細化具有一定的作用。寶鋼1號、2 號燒結機分別于2008 年6 月和2008 年3月實施了上述措施。該措施實施后,在一定程度上減輕了固體燃料粒度波動對燒結過程的影響,穩定了物料條件,降低了固體燃耗。在配礦條件變化不大的情況下,1 號、2 號燒結機的固體燃料單耗分別從實施前的
1) 在寶鋼燒結生產中,固體燃料的破碎存在波動性較大,人為影響大的特點。而固體燃料粒度波動,對燒結過程有較明顯的影響。
2) 統計表明,寶鋼1 號、2 號燒結機的固體燃料粒度波動范圍在113~
3) 通過生產參數的變化和燒結煙氣成分在線分析,能及時而準確地判斷出固體燃料粒度波動的情況,為采取適當的優化操作措施提供準確的依據。
4) 寶鋼燒結的生產實踐表明,通過添加水優化控制、熱量補償技術、部分風箱切換和抽風風量調整等措施,有效地減少了固體燃料粒度波動對燒結過程的影響,取得了較好的效果。
參考文獻
[ 1 ] 寧天興等1 寶鋼燒結生產設備[M]1 北京:冶金工業出版社,1997107 :36 - 371
[2 ] 傅菊英,蔣濤等1 燒結球團學[M]1 長沙:中南工業大學出版社,1996102 :281
從圖1 和圖2 可看出,兩臺燒結機的固體燃料平均粒度基本是在
率等) 帶來影響,使混合料的密度、空隙率、堆積密度等參數發生變化,從而引起燒結添加水系統的波動,局部出現潤濕不充分或過度潤濕,導致整個混合料的原始透氣性出現不均勻現象。在點火階段,粒度較小的炭粒迅速燃燒,而粒度較大的炭粒燃燒速度較為緩慢,這種情況就是燒結燃燒帶橫向分布不均的原因之一。固體燃料粒度的波動造成料層中的固體燃料燃燒動力學和熱力學條件相應發生變化,從而影響燃燒速度和炭燃燒的產物[2 ] 。
國內眾多燒結廠技術人員都在研究固體燃料的粒度及粒級組成在什么范圍內是最恰當的。比如,武鋼一燒研究表明,在一燒生產條件下,焦粉中<
3 固體燃料粒度波動的辨別
結合寶鋼燒結工序的實際情況和現場操作經驗,我們采取兩個步驟對固體燃料粒度波動進行推斷。第一步:根據混合料水分、BTP 溫度和風箱負壓等控制參數在短時間內的變化,來推斷固體燃料粒度波動的大致范圍。利用設在混合料槽里的中子水分計,測量出通過一二混加水后的燒結混合料水分值。在添加水量未調整的情況下, 其水分實測值波動范圍大體在±011 %。若生產過程中水分實測值波動超過±011 % ,多數是由固體燃料粒度波動所致。粒度波動幅度越大,水分波動幅度也越大。由于固體燃料粒度波動,影響到燒結過濕層及燃燒帶的厚度和分布,造成BTP 溫度和負壓的短時間波動。在燒結用勻礦大堆、燒結機速、料層厚度等參數未發生改變的前提下,若短時間內,BTP溫度和負壓出現較大幅度的變化,就可以考慮從固體燃料粒度波動的角度進行分析。第二步:借助氣體分析儀,在線測定燒結廢氣中CO、CO2 的含量,從而較準確地判斷固體燃料粒度波動的實際情況。燒結廢氣中CO/ (CO + CO2)比值稱為燃燒比,通常用這個比值來衡量燒結過程中碳素化學能的利用情況。燃燒比大,則碳素利用差,燒結過程中還原性氣氛較強。燃燒比小,則碳素利用好,燒結過程氧化性氣氛較強。在燒結過程中,還原性氣氛和氧化性氣氛都是存在的,只是在不同的階段和時間某種氣氛占主導位置。根據固定碳的燃燒機理,在燒結過程中,我們只要考慮碳燃燒的兩類主要反
應:
C + O2 = CO2 + 3218 kJ / kg (1)
在燒結機速和料層厚度穩定的情況下,固體燃料粒度和配碳量是影響燃燒比的主要因素。配碳量一定時,固體燃料粒度就是影響燃燒比的主要原因。固體燃料粒度的波動與燃燒
比的變化存在一定的相關性。
我們采用氣體分析儀(型號: ZKJ FM03 -YUCHC - HJNJNLV - AA8) 對燒結廢氣中的O2 、CO、CO2 含量進行在線監測,較迅速而準確地判斷出燒結過程中固體燃料粒度變化的情況,從而更好的對燃料破碎系統進行控制。根據燃料粒度檢測值和燒結廢氣中燃燒比測定值統計,得出兩者之間的線性回歸關系如下:
1 號燒結機為:燃燒比= 01398 - 01185 ×固體燃料粒度(R2 = 8912 %)
2 號燒結機為:燃燒比= 01347 - 01154 ×固體燃料粒度(R2 = 8415 %)
在線檢測燒結廢氣的燃燒比,彌補了燃料粒度檢測的滯后性,利用回歸公式便能及時掌握固體燃料粒度的大小和波動情況,為采取適當的優化操作措施提供了準確的依據。
4 優化控制措施及效果
結合寶鋼燒結固體燃料粒度波動的范圍和粒度分布維數k ,定義基準粒度為
4.1 添加水優化控制
焦炭和無煙煤破碎后,其形狀多種多樣,假設其為球形結構(不規則的顆粒也可轉換為等體積的球形結構) 。根據球形顆粒的體積和表面積公式,得出球形顆粒的比表面積公式:
球形顆粒的體積: V =π/6 d3p
表面積: S =πd2p
比表面積: a球= S/V=6/dp
式中: dp 為平均粒徑。
根據寶鋼固體燃料粒度波動的范圍,分別計算出不同粒度下焦粉顆粒的比表面積與基準顆粒比表面積的差異百分比(見表1) ;再結合焦粉粒度分布k 值和固體燃料配比C ,得出固體燃料粒度波動時,添加水量變化的指導值( △V) ,△V = 比表面積差異百分比×配碳量×相似度k。
以固體燃料配比314 % ,315 % ,316 %三個水平為例,當燃料粒度在112~118mm 范圍內波動時(取k = 014) ,添加水量變化指導值△V列于表2 。
4.2 熱量補償優化控制
固體燃料粒度波動,導致了炭粒燃燒速度發生變化,直接影響到燒結料層中各位置溫度水平發生變化。燃料粒度較大時,在相同料層水平達到的最高溫度較低;而粒度較細,則燃燒速度快,熱能集中,達到的溫度就較高。因此,在實際生產中,我們會參考固體燃料粒度的變化情況,對其配比進行適當微調,以進行熱量補償。在寶鋼2008 年的燒結配礦條件及機速、層厚條件下,其大致規律如表3 所示。
延伸閱讀
- 上一篇:鞍鋼燒結優化配礦研究 下一篇:鋼鐵行業燒結余熱發電技術