葉建軍 崔 強 張規華
摘要:先后在新線進行了多輪次工藝試驗和工藝改進, 根據新線裝備條件在短時間內確定了新線工藝,取得良好的效果, 性能合格率達到較好水平。
關鍵詞:工藝確定 工藝試驗 分析改進
前言
舞鋼公司自2003年批量生產壓力鋼管用低焊接裂紋敏感性高強鋼WDB620以來, 由于設備能力不足和工藝執行復雜等問題, 性能合格率始終很低, 達不到性能合格率92% 的要求。為此,新線建成投產后, 開始在新線進行控軋型WDB620( 50mm )鋼板的試生產, 旨在摸索控軋型WDB620在新線的生產工藝, 提高工藝的適應性, 減少操作的復雜程度, 提高鋼板的性能合格率。
先后在新線進行了多輪次工藝試驗和工藝改進, 在短時間內確定了新線工藝, 取得良好效果,性能合格率達到了95. 03%的最好水平。
1 工藝制訂
WDB620屬低C 貝氏體高強鋼, 在老線生產成分設計的前提下, 該鋼對加熱、軋制規程和軋后ACC 冷卻均有較高要求。新線四輥軋機最大軋制壓力達86 000 kN, 30~ 50mm厚鋼板最大水冷速度達20 ℃ / s, 較老線均有較大提高。因此工藝總體設計與老線相比重點做了以下調整。
1. 1 冶煉采用T i脫O 工藝, 利用高溫形成微細
的T i2O3 質點增加對晶界的釘扎作用, 減弱鋼板焊接熱影響區再熱循環晶界粗化, 提高可焊性。
1. 2 根據低C 貝氏體鋼的特性, 優化成分, 對于35mm厚鋼板進行去B、Ni、V試驗。
1. 3 軋制規程不再采用∀型控軋, 改用#型控軋工藝, 提高再結晶區和非再結晶區軋制道次壓下量, 細化晶粒, 從而放寬對#階段開軋溫度的限制, 減少等溫時間。
1. 4 簡化生產工藝, 進行軋后堆垛緩冷替代軋后回火熱處理工藝。
1. 5 研究鋼中B 元素對沖擊韌性的影響, 同時進行厚板去B、加C r試驗和其它工藝改進試驗。
2 工藝試驗
新線試軋首先圍繞改進工藝進行, 軋制工藝全部采用#型控軋, 重點進行了厚度35 mm 以上鋼板的工藝試驗, 在工藝試驗的同時穿插進行了成分調整試驗, 先后試驗了含B、不含B、去B 加C r+ N i三種成分, 試驗的目的是提高鋼板- 20 ℃低溫沖擊韌性, 爭取做到 50 mm 鋼板熱軋態和回火態- 20 ℃ 沖擊功均勻穩定, 成分調整主要是圍繞B對鋼板低溫沖擊韌性的影響進行的。
2. 1 試驗成分
WDB620鋼的試驗成分見表1。
2. 2 具體工藝試驗
2. 2. 1 第1階段
試軋規格30 mm、40 mm、46 mm, 坯厚250mm。成分為老線成分。試驗目的: 采用老線的成分和坯料, 初步試驗新線設備能力和效果。工藝特點: #階段開軋溫度 870 ℃ , 晾鋼厚度2. 5~ 3 T; 終冷溫度 530 ℃ , 冷速∃22 ℃ / s、30mm、40 mm 堆垛, 46 mm未堆垛。結果: 30mm、40mm強度超標, - 20 ℃ 沖擊不均勻; 46 mm 強度690MPa, 熱軋態- 20 ℃ 、- 40 ℃ 沖擊合格, 回火態- 40 ℃ 沖擊不合格。原因分析: 含B鋼組織中的粗大粒貝影響控軋態和回火態韌性。
2. 2. 2 第2階段
試軋規格28 mm、46 mm、48 mm, 坯厚300mm。試驗目的: 針對老線成分強度偏高, 韌性低,且回火后韌性惡化, 強韌性匹配不合理, 決定不加B 冶煉兩爐, 其中一爐加入N i 以便做對比。采用兩種軋制冷卻工藝, 一種為: Ⅱ階段開軋溫度≤860℃, 晾鋼厚度2. 5 ~ 3 T; 終冷溫度≤530℃ ,冷速25 ℃ / s。其結果是最高強度605MPa, 控軋態- 60℃ 沖擊250 J以上, 回火態強韌性無變化;另一種為: 軋制溫度提高30 ℃ , 其它工藝不變, 其結果是最高強度620MPa, 熱軋態- 60 ℃ 沖擊250 J以上, 回火態強韌性無變化。含N i對韌性改善不明顯。原因分析: 無B 成分組織轉變中生成大量鐵素體, 即使調整終軋溫度和回火處理也不能提高強度指標。
2. 2. 3 第3階段
試軋規格30mm、40mm, 坯厚200mm, 成分;含B 或含B + V。試驗目的: 針對第二輪去B 試驗鋼板的強度指標不能滿足標準要求, 決定少量添加B, 且其中一爐加入適量V, 以便對比。工藝特點:Ⅱ 階段開軋溫度≤880℃ , 晾鋼厚度2. 5~ 3T; 終冷溫度 ≤530 ℃, 冷速25 ℃/ s。結果: 強度偏高但合格, 熱軋態30 mm 厚板- 20℃、- 40℃沖擊合格; 40mm厚板, - 20℃沖擊合格, 回火態30 mm 厚板- 20℃沖擊合格, 40 mm厚板不合格。20 mm、40 mm、46 mm厚度含B+ V鋼板, #階段開軋溫度≤810℃ , 晾鋼厚度2. 5~ 3T; 終冷溫度 ≤580℃ , 冷速6~ 10 ℃/ s。結果: 強度適中, 熱軋態20 mm 厚板- 40℃沖擊較高, 40mm厚板- 20℃沖擊不合格。原因分析: #階段開軋溫度不是影響沖擊的主要因素, 原料坯厚小,Ⅰ階段變形量不足是影響沖擊的主要因素。
2. 2. 4 第4階段
試軋規格44 mm, 坯厚300 mm, 成分為含B或去B加入適量C r、N i、V。試驗目的: 在無B 鋼的試驗基礎上, 增加強化組分, 提高強度指標。工藝特點: Ⅱ階段開軋溫度≤850℃ , 晾鋼厚度2. 5~ 3 T; 終冷溫度≤500℃, 冷速18℃ / s。結果:熱軋態無B、含B 鋼強度適中, 0 ℃ 沖擊功≥250J, - 20℃沖擊不穩定; 回火態0℃沖擊不穩定,無B、含B 鋼差別不明顯。原因分析: 無B 成分組織轉變中生成少量鐵素體, 強度韌性均得到改善,含B 鋼沿厚度方向組織不均勻, 粒貝較多。
2. 2. 5 第5階段
試軋規格44 mm, 坯厚300 mm, 成分為去B加入適量C r、N i、V。試驗目的: 在第4 階段的基礎上降低C r含量0. 10%。工藝特點: Ⅱ階段開軋溫度≤ 870 ℃, 晾鋼厚度3 T; 終冷溫度≤ 500℃ , 冷速15℃/ s。結果: 熱軋態強度適中, 0 ℃沖擊功≥150 J, - 20 ℃ 沖擊穩定; 系列回火態0℃沖擊改善。原因分析: 組織轉變中生成貝氏體+鐵素體, 強度韌性均改善, 粒貝不同回火溫度分解不同, 韌性改善。
3 試驗結果
3. 1冶煉采用T i脫O 工藝在操作上是可行的,對冶煉爐次進行夾雜物分析, 結果B 類夾雜物為2. 0級, 略高, 但該類夾雜物沿軋制方向延展較小, 對沖擊韌性的影響有限, 而且采用T i脫O 工藝后, 原加熱工藝相應調整, 最高加熱溫度從1 200 ~ 1 220℃提高到了1 260 ~ 1 280 ℃ , 使WDB620鋼坯的加熱可按大生產工藝控制, 降低了加熱溫度對性能的影響。焊接性能因為微細T i2O3 對熱影響區粗晶區晶界的釘扎作用而明顯改善。
3. 2 含B 鋼采用#型控軋方式可生產35 mm 以下的鋼板, 而且可用200 mm連鑄坯軋制, 當第%階段壓下量∃50%, 第#階段壓下量∃60% 時, 即可保證控軋板強度適中, - 20 ℃ 沖擊功均勻穩定且均值> 200 J, 從而大大提高了原料的適用范圍。200mm 連鑄坯軋制 35 mm 鋼板的典型實物性能見表2。
3. 3 無B 無C r鋼軋制的35 mm以下鋼板, 沖擊雖可達到- 60 ℃ 均值> 200 J, 但強度始終難以達到620MPa以上, 金相組織觀察該成分鋼板的典型組織為95% PF + 5% P, 鐵素體的晶粒度為11~ 12級, 由此可見無B 鋼沖擊韌性的改善是由于組織中大量PF的生成, 以及無B 硬化第二相數量減少共同作用的結果, 這也是這種成分的鋼板在回火之后強度和沖擊功不發生變化的原因。
3. 4 35 mm 以上規格含B ( 07305520No)和無B+ C r+ N i( 07305521No)鋼采用#型控軋工藝, 具體工藝見表3、性能結果見表4。從表3、表4可看出含B鋼0 ℃ 沖擊功均在260 J以上, - 20 ℃ 沖擊仍不穩定; 無B + C r+ N i鋼熱軋態強度適中, 0 ℃ 沖擊功均在200 J以上, 且- 20 ℃ 沖擊穩定。
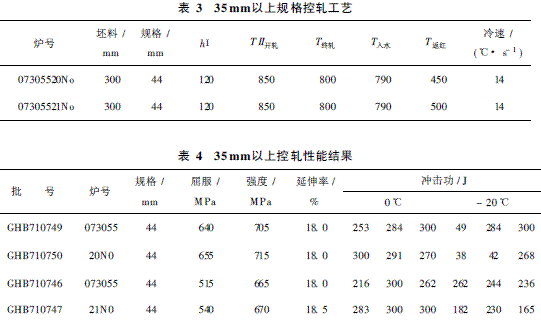
3. 5 軋后堆垛緩冷與不堆垛相比, 鋼板的性能無明顯差別(可能與每次所軋塊數較少有關), 但35mm以上厚度鋼板下冷床仍執行單塊平鋪晾鋼。
4 問題討論
4. 1 控軋工藝對沖擊韌性的影響
采用Ⅱ型控軋和Ⅲ型控軋對鋼沖擊韌性的影響不明顯, 兩種軋制方式的最大區別是Ⅲ 型控軋在γ未再結晶區和所謂的“兩相區”進行兩次軋制, 而#型控軋則在γ未再晶區終軋至結束。對于含B低碳貝氏體鋼而言, 其含B 約0. 001% ~0. 002% [ 1] 時, 由于B 在變形γ區晶界的強烈偏聚阻止了F的形核長大, 在軋制空冷過程中很難生成F, 從含B 鋼全厚度金相分析中也很難發現F的存在。因此實際上就不存在兩相區軋制的可能, 即兩種方式均是在γ未再晶區軋制, 只是Ⅲ型控軋多了一個在γ未再晶區下沿軋制的過程,這也是對沖擊韌性影響不明顯的原因所在。
4. 2 形變量對沖擊韌性的影響
對于厚度 35 mm 鋼板, 無論采用200 mm鑄坯還是300 mm 鑄坯, 低溫沖擊韌性均可達到150 J以上, 但采用300 mm 鑄坯軋制的鋼板低溫韌性明顯優于200 mm 鑄坯, 主要是因為大變形時, γ晶粒細化充分, 變形帶增加, 位錯數量增加,增大了晶內形核和相變B形核數量, 相變后組織均勻[ 2] , 從而提高了低溫沖擊韌性。考慮到總壓縮比和保證控軋各階段變形量的要求, 35mm以上要求- 20 ℃ 沖擊韌性的鋼板應采用260 mm 以上連鑄坯生產, 以確保高溫再結晶區變形70% 以上, 非再結晶區軋制變形60% 以上。
4. 3 不同成分對沖擊韌性的影響
采用含B成分生產厚度> 35mm鋼板的0 ℃沖擊較高, 但熱軋態- 20 ℃ 沖擊和回火后0 ℃ 沖擊不穩定, 這是因厚板沿厚度方向上冷卻速度降低, 而且B元素在高溫態阻止了過冷γ分解, 增大了過冷γ的穩定性, 增大了粒貝組織的數量,并且影響了粒貝上的MA 的大小、形狀、數量、分布等特性, 從而影響沖擊韌性。而對低C 貝氏體鋼, 低溫沖擊韌性主要由貝氏體鐵素體上分布的MA 的特性和貝氏體板條束寬度兩個因素決定的。貝氏體板條束寬度的影響在光鏡和掃描電鏡下是無法分辨的, 但可借助光鏡下MA 的分布形態來判斷[ 3] , 對WDB620 鋼沖擊的影響從電鏡中觀察后認為改變和控制粒貝上的MA 的大小、形狀、數量、分布即可達到控制沖擊韌性的目的, 改善MA 特性的同時貝氏體板條束尺寸也可得到改善。
采用無B 加C r、N i生產厚度大于35 mm 厚板, 組織分析熱軋態為B + F, F呈等軸狀, 沿γ晶界呈網狀析出, 包圍轉變成的粒貝組織, 粒貝中MA 相數量、大小、分布明顯較含B 鋼減少, 因此沖擊韌性大大改善。但在該低C 成分下, A r3升高[ 3] , 軋制中820 ℃ 即生成等軸F, 強度難以保證, 因此必須通過強冷來改善。
4. 4 B 元素對沖擊韌性的影響
B元素對低碳貝氏體鋼低溫沖擊韌性的影響在文獻中鮮有分析, 但從新線的生產實踐中看出:即使含B 鋼28mm、32 mm 鋼板的沖擊韌性達到300 J以上, 厚板沖擊韌性不高的原因與鋼中是否含B 有一定的關系, 尤其是是含B對γ穩定性[ 3]和相變后MA特性的影響。而厚板與薄板的最大區別是晶粒細化程度和冷速的不同, 正是這兩點的不同造成了粒B 組織中MA 的大小、形狀、數量、分布差異, 而并非僅是B 元素相變時在γ晶界偏聚的影響。這也是低C 貝氏體鋼連續冷卻組織轉變的特性之一。
4. 5 設備能力對沖擊韌性的影響
相關文獻提出, 當低碳貝氏體鋼冷卻速率≥20 ℃ / s時, 沖擊韌性可大大改善[ 1] 。但舞鋼新線MULPIC 中的DQ 冷卻水在試制過程中常不能正常使用, 影響到冷卻工藝參數的執行, 尤其對厚板冷卻效果影響較大, 表現為實際出水返紅溫度與設定溫度差約60~ 80 ℃ , 上下表溫差加大, 得不到預期的組織, 而且沿厚度方向組織不均勻, 影響沖擊韌性的提高。
5 軋制工藝的確定
5. 1 成分選擇
經實驗證明厚度 35 mm 含B 鋼在合理的加熱、軋制及水冷制度下, 能夠進行合理的低C貝氏體組織控制, 鋼板性能穩定, 且該成分在原成分的基礎上取消了N i、V 的加入, 達到了降低成本的要求, 因此該厚度規格鋼板選擇含B成分。厚度> 35 mm 厚鋼板采用無B + C r+ N i+ V成分, 通過優化組織, 生成一定數量的F 相來提高沖擊韌性。最終成分確定見表5。
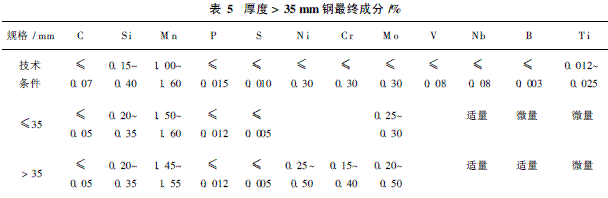
5. 2 軋制規程
坯料厚度≥200 mm, 采用#型控軋, 與老線相比, 提高終軋溫度約30 ℃ , 具體軋制工藝參數見表6。
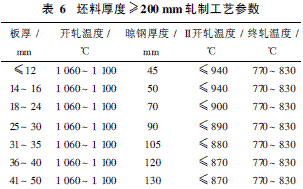
5. 3 水冷工藝
水冷工藝執行見表7。
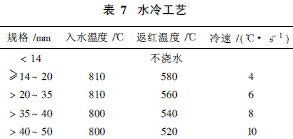
6 大生產驗證
工藝確定后進行了WDB 620的批量生產, 共生產檢驗873批, 初驗合格830批, 初驗性能合格率95. 03% , 其中 35 mm鋼板生產檢驗726批,初驗合格692批, 初驗性能合格率95. 3% , > 35~ 50mm鋼板生產檢驗147批, 初驗合格139批,初驗性能合格率94. 55%, 均較工藝改進前有大幅度提高。部分鋼板性能檢驗結果見表8。
7 結論
新線WDB620已基本實現了發揮新線設備能力, 簡化生產工藝、改∀型控軋為#型控軋、擴大工藝范圍, 控軋生產厚度達到50mm; 取消合金N i、V 加入, 降低生產成本, 噸鋼節約成本800元以上; 實現了改善鋼板不平度, 消除板型瓢曲等轉產目標。
參考文獻
1 翁宇慶. 超細晶鋼. 冶金工業出版社.
2 劉云旭. 金屬熱處理原理. 機械工業出版社.
3 賀信萊, 等. 高性能低碳貝氏體鋼. 冶金工業出版社.