武鋼4號高爐冷卻壁破損的原因
來源:陳令坤 宋木森 |瀏覽:次|評論:0條 [收藏] [評論]
武鋼4號高爐冷卻壁破損的原因
陳令坤 宋木森
(武漢鋼鐵集團公司)
摘 要:根據武鋼4號高爐破損調查的結果,分析了冷卻壁破損的原因,認為冷卻壁破損不但與鑄造質量不過關有關,而且與發展邊緣的高爐操作制度有關,與高爐操作爐型有關。
關鍵詞 大型高爐 冷卻壁 高爐操作
1 引言
武鋼4號高爐(2516m3)第三代爐役于1996年10月28日開爐,2006年7月3日停爐大修,連續生產9年9個月。其間沒有進行中修,也沒有停爐進行爐內噴補,累計生產生鐵1764.48萬t,單位爐容產鐵7013.04 t/m3。武鋼4號高爐第三代爐役設計壽命為10年,采用了多項先進技術,如軟水密閉循環冷卻技術、QT400—20型球墨鑄鐵冷卻壁、無料鐘爐頂裝料設備、內燃式高溫熱風爐、高爐過程計算機控制系統、雙出鐵口等。高爐內襯采用了當時國產優質耐火材料,如微孔炭磚、半石墨炭磚、SiC磚、微孔鋁碳磚、磷酸浸漬粘土磚等。
4號高爐冷卻系統的工作狀況盡管優于國內投產的其他同類型高爐,但和早先投產的5號高爐相比,在高爐長壽方面存在許多不足。4號高爐從2000年起冷卻壁水管損壞較多,2002年冷卻壁水管損壞最多,達24次,是冷卻壁損壞的高峰時期,對當年的生鐵產量影響較大。為弄清冷卻壁破損的主要原因,同時分析操作對高爐壽命的影響,4號高爐大修期間,對冷卻壁進行了破損調查研究。
2 冷卻壁破損調查結果
停爐后觀察,爐缸爐底1~6段冷卻壁保持完好,沒有損壞漏水現象。
爐身7、8、9三段冷卻壁破損最嚴重,勾頭全部損壞,鑄鐵體掉光,僅剩少量露出的水管;西面15號風口上方和北面21號風口上方有4~5塊冷卻壁損壞,上下3段連成一片,冷卻壁鑄體全掉光,每塊冷卻壁的4根水管仍然存在.多數未燒穿,可以繼續通水冷卻。其他方位多處有1~2塊冷卻壁露出水管、鑄體掉光的情況。大部分冷卻壁雖有冷卻壁存在,但水管以內的鑄鐵體已接近侵蝕光,水管已有部分露出,如圖1所示。
10~12段勾頭鑄鐵體掉光,水管露出,冷卻壁完整,水管未露出,但有明顯侵蝕,鑄體減薄,局部可見到鑲磚,如圖2所示。
13~15段冷卻壁完好,仍有磚襯,下部磚襯較薄,上部磚襯較厚,與勾頭平,勾頭完好。
16段光面冷卻壁完好無損。
3 球墨鑄鐵冷卻壁使用狀況解剖分析
國內外的研究都證明,高爐長壽主要取決于設計水平、設備及耐材質量、施工質量、原燃料條件、高爐操作及維護水平。武鋼4號高爐大修時采用了和5號高爐一樣的技術,但獲得了不同的壽命,這非常值得研究。
3.1 高爐設計施工中存在的問題
為滿足公司鐵、鋼平衡,1996年4號高爐大修工期非常緊張。高爐冷卻系統未試水就砌磚了,造成水系統漏水,爐缸遭浸泡,高爐施工及砌筑質量存在隱患;同時高爐爐身下部、爐腰部位采用了氮化硅結合碳化硅磚,這種磚掛渣性較差。這些問題都給高爐冷卻壁壽命造成了不好的影響。4號高爐冷卻壁破損情況見表1。
3.2 冷卻壁及冷卻壁水管取樣分析
為分析冷卻壁破損原因,對殘存冷卻壁進行了取樣解剖分析。檢測的內容主要有:拉力強度、屈服強度、延伸率和面收縮率;化學成分;金相組織、鐵素體含量、石墨形態和石墨球化級別;水管檢驗金相組織,外表有無滲碳,內部有無氧化。
所取的冷卻壁試樣主要有:15段一塊,西北面;11段一塊,西面;9段兩塊,西北面,9段一2號樣僅有上半部,下部已燒掉;8段一塊,西面;7段一塊,西面。將所取冷卻壁試樣,從中間切斷,取下一片試樣,分內、中、外取9個拉力試樣,3個化學分析樣,3個金相試樣,1個水管樣,然后分別檢測。這里假定冷卻壁外表樣和中部樣可代表冷卻壁使用前的性能。冷卻壁檢測結果見表2~4。
冷卻壁工作面的金相組織檢測結果表明,冷卻壁表面有嚴重滲碳并伴有氧化,脆性增加,是產生裂紋的源頭。冷卻壁內表層典型的滲碳和氧化腐蝕樣,如9段冷卻壁內表層,內部組織和內表面的金相組織對比見圖3和圖4。從圖中可清楚看到,內表層金相組織鐵素體80%全部變為萊氏體,稍深部位全部變成珠光體,表明工作面有嚴重滲碳,材質變硬、變脆,容易開裂。當內表面滲碳,性能變脆,裂紋產生時,如果鑄體內部性能也不好,強度很低,延伸率也很低時,裂紋很容易深入冷卻壁內部,裂紋擴大,甚至斷裂。當內部性能好時,可以阻止這種裂紋擴大,使裂紋僅在表面產生,不致于影響使用壽命。這種表面滲碳、氧化引起金相組織變化、脆性增加是必然的,不可避免。但其深度并不很大,曾研究過最深的約15 mm,只要鑄體內部材質性能優良,這種裂紋不致擴大,就不會影響整塊冷卻壁的使用壽命。
對15、11、9、9—2、8、7等6段冷卻壁解剖時,每塊冷卻壁取水管一個,進行金相分析,分析水管外表面是否滲碳,內表面是否氧化。檢測結果表明,水管組織為鐵素體 珠光體,水管的內外表面層都有脫碳層,珠光體消失,外表面脫碳層深度約為0.237~0.53 mm,內表面脫碳層深度約為0.742~1.467mm。
水管外表面在鑄造過程中沒有增碳,表明防滲碳涂料正常,效果良好。水管內部腐蝕很輕微,水垢很薄,僅看到薄薄一層沉積物。顯微鏡下可見內表面有輕微的腐蝕層和水垢(見圖5)。水管內表面有脫碳現象,其原因仍是水中含有少量氧氣所致。
根據冷卻壁解剖的性能檢測結果和球墨鑄鐵的性能質量要求,可以看出6塊冷卻壁僅15段內層1個樣達到380MPa,延伸率為23.5%,其他無一個合格。延伸率多數為4%~8%,少數10%~12%;石墨球化級別3級少,沒有1~2級,多為4~5級;鐵素體含量僅一個樣達到90%,其余多為65%~80%,最低的僅30%一40%。
由于冷卻壁石墨球化很差,延伸率很低,金相組織中大量珠光體甚至萊氏體,即滲碳體,類似灰鑄鐵。使用過程中大量開裂破損,其開裂狀況類似灰鑄鐵冷卻壁,裂紋大且多,裂紋穿透冷卻壁分割成很多碎塊而脫落,是冷卻壁損壞、脫落留下水管的根本原因。
4 高爐操作與鐵冷卻壁破損較快的關系
4.1 根據原料特點,利用布料抑制高爐邊緣氣流發展
球墨鑄鐵冷卻壁的力學性能,拉力強度、延伸率和面收縮等,受溫度影響很大。研究表明,球墨鑄鐵溫度在400℃以下,性能保持不變,溫度再升高,拉力強度迅速下降;延伸率也在400℃開始產生變化。因此,球墨鑄鐵冷卻壁內表面的工作溫度不應超過400℃,當溫度過高時,將縮短使用壽命。高爐生產中,將冷卻壁內表面溫度控制在400℃以下。在實際的高爐操作中,一旦外部原料條件發生較大的變化,高爐冷卻壁熱面溫度經常超過400℃以上,這將導致冷卻壁工作性能下降。
4號高爐爐役前期一直采用的是維持適當邊緣氣流、開發中心氣流的兩股氣流操作模式來選擇布料矩陣,煤氣利用水平不高,CO2只有18.4%左右,主要的代表矩陣是
。進入2002年后,自3月開始,高爐用料結構及爐料質量發生比較大的變化,燒結礦質量差,焦炭缺口大,大量卸焦,外購焦又多,焦炭質量難以保證。高爐操作風量不穩,難以組織高產,2002年下半年二燒質量有所改善。但不久后的5座爐子同時生產,使原、燃料全面緊張,卸焦量又有所增加,焦炭質量極不穩定,給操作帶來較大困難。特別是2002年8月煙煤一期工程投入運行,實現煙煤混噴。煤比提高后,初始邊緣氣流發展,許多情況下冷卻壁溫度達到400℃以上,以致冷卻壁損壞較多,冷卻壁損壞加劇。2002年全年共損壞冷卻壁水管24次。2003年8月開始適當抑制邊緣氣流,最終摸索出抑制邊緣氣流、發展中心氣流的布料制度。2003年1月21日,首先在武鋼煉鐵廠采用錯角位布料
,2003年10月最終定為
。采用這種布料制度后,邊緣氣流適當壓抑,氣流穩定,使不穩定的氣流對爐墻沖刷減少,確保了邊緣焦層有一定寬度及適宜的邊緣礦石抑制邊緣氣流,使邊緣氣流更為穩定。中心、中間帶的煤氣流比率相對穩定,保證了邊緣、中心兩股氣流合理分布,煤氣利用水平大幅度提高,CO2達19.3%,最高可達22.2%,損壞冷卻壁次數逐年減少。
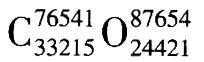
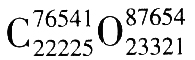
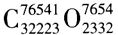
4號高爐冷卻壁過早損壞的原因,與4號高爐前期邊緣氣流過分發展,冷卻壁熱面溫度較高有一定關系,是損壞較快的原因之一。也說明一代高爐從投產之日就應該重視保護冷卻壁,嚴格控制邊緣氣流過分發展。
4.2 穩定爐型、減少爐型波動
高爐操作爐型的頻繁變化會使冷卻壁內表面的溫度產生波動。由于溫度的波動,使冷卻壁變形,內應力發生變化,天長日久,反復發生,產生熱疲勞,致使冷卻壁破損。盡管球墨鑄鐵具有優良的性能,也還是應該控制冷卻壁急冷急熱的次數。國內外冷卻壁使用經驗表明,球墨鑄鐵冷卻壁急冷急熱次數超過800次,就會出現破損。通過4號高爐冶煉專家系統的檢測,在原料波動大時,高爐一天之內渣皮脫落的次數最多達到10多次之多。經推算,從2000年以后,冷卻壁將開始大量破損,高爐實踐經驗也驗證了這種推斷。
一般情況下,冷卻壁溫度應控制在60~90℃的范圍內。一旦低于50℃,則邊緣就有結厚的跡象。應恰當發展邊緣氣流,如平均溫度高于120℃,或一天之內有多個點溫度達到250℃以上,就說明邊緣氣流偏旺,渣皮不穩,爐型維護不利,就應采取恰當措施進行改進。
基于上述認識,在球墨鑄鐵冷卻壁制造中,必須十分重視拉力強度和延伸率這兩項性能,千萬不能放松要求。經多次冷卻壁破損調查表明,性能優良的球墨鑄鐵冷卻壁即使部分被燒壞,殘留下的部分冷卻壁也不會開裂。4號高爐球墨鑄鐵冷卻壁大量開裂,其原因就是拉力強度和延伸率遠未達到要求。解剖檢測表明,已接近灰鑄鐵的性能。因此,必須吸取教訓,引起高度重視,冷卻壁的制造必須做到精益求精。
4.3 確保高爐爐墻形成穩定的操作渣皮,減少爐料對爐墻的磨損
從4號高爐冷卻壁的破損情況看,除開裂破碎外,高溫燒蝕和磨損是另一嚴重侵蝕狀況。由于高溫燒蝕和磨損,冷卻壁鑲磚和鑄體逐漸減薄,減薄的程度很大,很多冷卻壁鑲磚已全部侵蝕光,能見到水管露出。從解剖的厚度變化(見表5),可以看出燒蝕和磨損的嚴重程度。由表5中可見,15段冷卻壁保持原始厚度,11段冷卻壁雖然冷卻壁勾頭保留和壁體尚有鑲磚,但其厚度已減薄15 mm。9段以下減薄的厚度加大,8段最大達100 mm,7段減薄程度小于8段。可見7、8、9段冷卻壁高溫燒蝕和磨損很嚴重。
表5 武鋼4號高爐冷卻壁的殘存厚度(取樣斷口)
對設計壽命20年的長壽高爐來講,這樣的燒損速度顯然是不能達到20年的壽命。其原因是鑄鐵冷卻壁熱導率偏低,冷卻強度不夠。當渣皮脫落時,渣皮不能及時生成形成保護層,致使冷卻壁燒損、高溫爐料和氣流磨損。因此,7、8、9三段冷卻壁應該使用銅冷卻壁,提高冷卻強度,才能滿足20年長壽高爐要求。
這種高溫燒蝕和磨損速度顯然與材質的性能有密切關系。強度低、延伸率低的球墨鑄鐵不僅會開裂,而且會成為碎塊脫落,必然加速破損速度。武鋼5號高爐壽命已達到16年,說明球墨鑄鐵冷卻壁在制造質量好的情況下是可以延長使用壽命的。
4.4 高爐操作過程中必須確保足夠的冷卻強度
4號高爐采用的軟水密閉冷卻系統由相對獨立的三部分組成,即高爐本體冷卻系統、爐底冷卻系統、風口及熱風閥冷卻系統。高爐冷卻壁全部采用球墨鑄鐵冷卻壁,水管采用書70×6mm的10號鋼管,設計水速1.6m/s,單根水量15 m3/h,總水量4410 m3/h。
爐役后期,通過降低進水溫度,增加冷卻水量等措施確保高爐冷卻壁的冷卻能力,使冷卻壁鑄體脆裂脫落后水管仍不壞,能繼續通水冷卻,對高爐后期的順行起了重要作用。
5 結語
(1)高爐長壽技術是一種綜合技術[1~2],它與設計、制造、材質、施工、原燃料條件及高爐操作密切相關,應該嚴格按照技術要求重視每一個環節,否則高爐很難獲得長壽。
(2)武鋼4號高爐的冷卻壁破損與冷卻壁制造質量有很大的關系,高爐應該使用合格的冷卻壁,杜絕不合格產品安裝到高爐上。
(3)在重視設計、產品質量及施工的同時,應該充分發揮高爐上下部調劑的優勢,重視氣流控制,穩定操作爐型,減少渣皮的脫落,避免冷卻壁頻繁急冷急熱。
(4)在冷卻壁出現問題時,應想辦法確保冷卻壁的冷卻能力。
6 參考文獻
1 張壽榮.延長高爐壽命是系統工程,高爐長壽技術是綜合技術.煉鐵,2002(1):1—4
2 程樹森,楊天鈞等.長壽高爐設計指標及設計方案評價系統初探鋼鐵,2000(5):10一13
- 上一篇:攀鋼高爐出鐵場煙塵治理實踐 下一篇:首鋼2號高爐銅冷卻壁使用的體會
- [騰訊]
- 關鍵字:無